お客様の課題・ニーズ
自動車の樹脂部品の乾燥工程を設けた洗浄機において、従来は銅パイプを用いた乾燥を行っていました。
銅パイプを用いることによる問題点は、エア消費量に対する乾燥効率が悪いことです。エアコンプレッサー3台を使用し樹脂部品を乾燥していましたが、電気代やメンテナンス代など、ランニングコストが上昇しており、また、新ライン導入時にエアコンプレッサーを追加設置しないといけないなど、コスト面の課題が発生していました。
当事例のお客様は、機械構造を大きく変更することなく、低コストの改造により乾燥効率を向上させる方法を模索されており、当社にお声かけ頂きました。
提案内容
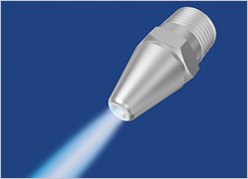
銅パイプは内部が直進構造で大気噴射後のエアーの減速が大きいため、エア消費量に対する乾燥効率が低下していました。そのため、大気噴射後に減速の少ない構造を持つエアジェットノズルを提案しました。
噴射距離200mmで、既存のパイプと同風速、かつ一番空気量の少ないノズルを選定しました。標準ノズルを形状変更なく納入すると乾燥工程の機械構造を大きく変更する必要があるため、既設パイプに取り付け可能な構造にカスタマイズすることを合わせて提案しました。
試作・評価試験
まず、当社試験装置で噴射距離200mmでの既設パイプの風速を測定し既設パイプと同様になるエアジェットノズルを選定しました。そして、噴射距離200mmの位置で風速・衝突力試験を実施することで、最適なノズルであることを確認しました。
ノズルをパイプに取り付けるため、形状をカスタマイズした特注エアジェットノズルの試作品を製作し、実機に取り付けテストを行い、乾燥具合とエア消費量の関係性をデータ化したところ、従来の銅パイプと比較し2/3のエア消費量に改善されたことが分かり、当ノズルにて導入させて頂きました。