Challenges
Previously, air blow from brass piping was adopted to machine with drying process for automotive plastic parts.
The issue with brass piping was low drying efficiency against air consumption.
Three air compressors were used for drying plastic parts, however, there was cost issue which was running cost.
Solution
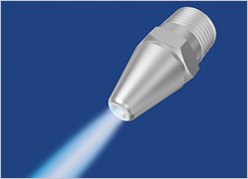
In brass piping, since large reduction of spray speed was occurred due to straight structure, drying efficiency was lower comparing with air consumption.
We selected air nozzle which can spray the same air speed with existing piping at spray distance 200mm and the lowest air consumption.
In addition, since a big change of the equipment was necessary in case of our standard shape, we customized our air jet nozzle to enable to install to current piping.
Trial
Firstly, we measured spray speed at spray distance 200mm at our factory and selected nozzle which sprayed the same speed.
And then, we confirmed that the air jet nozzle was suitable nozzle by actual measurement of spray speed and impact force.
After prototyping nozzle which was customized to enable to install to the current piping, the nozzles was installed to the equipment and tested.
The air consumption with our nozzle was only one-third, compared with the previous piping at the result of digitizing relationship with drying and air consumption. Because of the test result, our nozzle was adopted.